B777 Flight
Lufthansa Cargo flight LH8402, a Boeing 777-F, returned to land at Frankfurt International Airport (FRA), Germany after the cockpit crew noticed unreliable airspeed indicator readings. Prior to the departure on October 10, 2020, various scheduled maintenance tasks had been performed on the aircraft. Apr 06, 2016 PMDG Boeing 777 - Complex and realistic simulation of the Boeing 777 References Gregg F. Bartley - The Boeing 777 Fly-By-Wire Flight Control System, Ch. 11 The Avionics Handbook (2001 CRC Press). Jul 08, 2020 The Boeing 777-200ER flying to London that morning was registered N772AN, a tail code identifying it as a jet that’s been grounded since late March, according to flight-tracking site. Presented herein are Boeing 777-200ER aircraft operational usage data collected from 10,047 flights, representing 67,000 flight hours, recorded by a single international operator. Data are presented that will provide the user with statistical information on aircraft usage, ground and flight loads occurrences, and system.
Abstract
Airbus introduced full Fly-By-Wire (FBW) flight controls into their A320 in 1987 as the first civil commercial airliner to incorporate such a system. Boeing followed in 1994 with their wide-body, long-haul Boeing 777, albeit with a different philosophy. Today, some 20 years later, virtually every new commercial jetliner project involves some form of FBW flight control system.
In this article I will analyze the FBW System of the Boeing 777 (Triple Seven) from a pilot's point of view and with the help of a desktop flight simulation through a series of flight tests that will illustrate how the system works, how it makes the job of the pilot easier, and how it protects the aircraft's flight envelope.
This article was written as a read-along companion for my video-analysis below:
Table of Contents
Introduction
- Philosophy of the Boeing 777 FBW Flight Control System
FBW System Overview and Description
- Cockpit Controls
- System Architecture
- Operating Modes
Flight Tests
- Effect of Primary Flight Control Commands
- Effect of Trim Reference Airspeed (constant thrust)
- Effect of Thrust Changes (constant Trim Reference Airspeed)
- Turn Compensation and Bank Limit Protection
- Configuration Change Compensation
- Approach to Stall and Full Stall
Conclusion
Software
References
Introduction
Philosophy of the Boeing 777 FBW Flight Control System
Boeing intended their 777 to be flown just as a conventional jet aircraft. They wanted a 737 pilot (I will often use the 737 as an example of a conventional non-FBW aircraft throughout this article) capable of jumping into the flight deck of the 777 and still feel like 'home'. That's the reason why the cockpit controls for all four Degrees of Freedom (roll, pitch, yaw and thrust) remain unchanged from previous Boeing aircraft, that is: two sets of rudder pedals for governing the rudder (yaw axis), two 'yokes' consisting of control wheel for governing the ailerons, spoilers and flaperons (roll axis) and control column for governing the pitch axis and finally one set of thrust levers to control the engine's thrust output.
Boeing also designed its flight deck not only so it 'looks' like one of a conventional aircraft, but also so it 'flies' like one, moreover like an extremely 'well behaved' one. The key idea is that our FBW-ignorant pilot coming from the 737 wouldn't have to learn to fly all over. In fact, the 777 flies just like the trainer aircraft that Mr. Langewiesche had in mind when he wrote his beknown 'Stick and Rudder' (see reference 6). Our 737 pilot could fly the 777 without even knowing it's a FBW aircraft.
What is meant by 'well behaved' is a set of superior handling qualities that make the pilot feel like the aircraft is noble and easy to fly. The Boeing 777's FBW has an effect on these qualities as well through the use of Stability Augmentation features and Compensations of different nature. Its rating in the Cooper-Harper scale of handling qualities should be '1' or 'excellent'.
Finally and even more importantly, it's Boeing's philosophy that the FBW of the 777 lets the pilot be always in command of the airplane and have full authority over it in all situations. There's no computer the pilot can't override. The aircraft will warn the pilot should he be dangerously close to the limit of the aircraft's flight envelope and will also impose 'soft limits' to prevent the aircraft from exceeding those limits inadvertently, but the pilot will be able to fly the aircraft out of its envelope if he's determined enough to do so.
FBW System Overview and Description
Cockpit Controls
As mentioned before, cockpit controls consist of yokes, rudder pedals and thrust levers, just as in a conventional 737.
Unlike modern Airbus aircraft, in the 777 both the rudder pedals and the yokes are mechanically interconnected so that either pilot feels and sees what the other pilot is doing when he operates the controls. In addition, all flight controls are 'backdriven' by the Autopilot and/or Autothrottles when they are engaged, so as to keep the pilots in the loop and give them visual clues of what the Auto-Flight System is doing; the exception being the rudder pedals which will not be backdriven by the Autopilot except during an Autoland approach below 1500 feet. No matter what the level of automation is, any pilot can grab any control and manually override the Autopilot or Autothrottles.
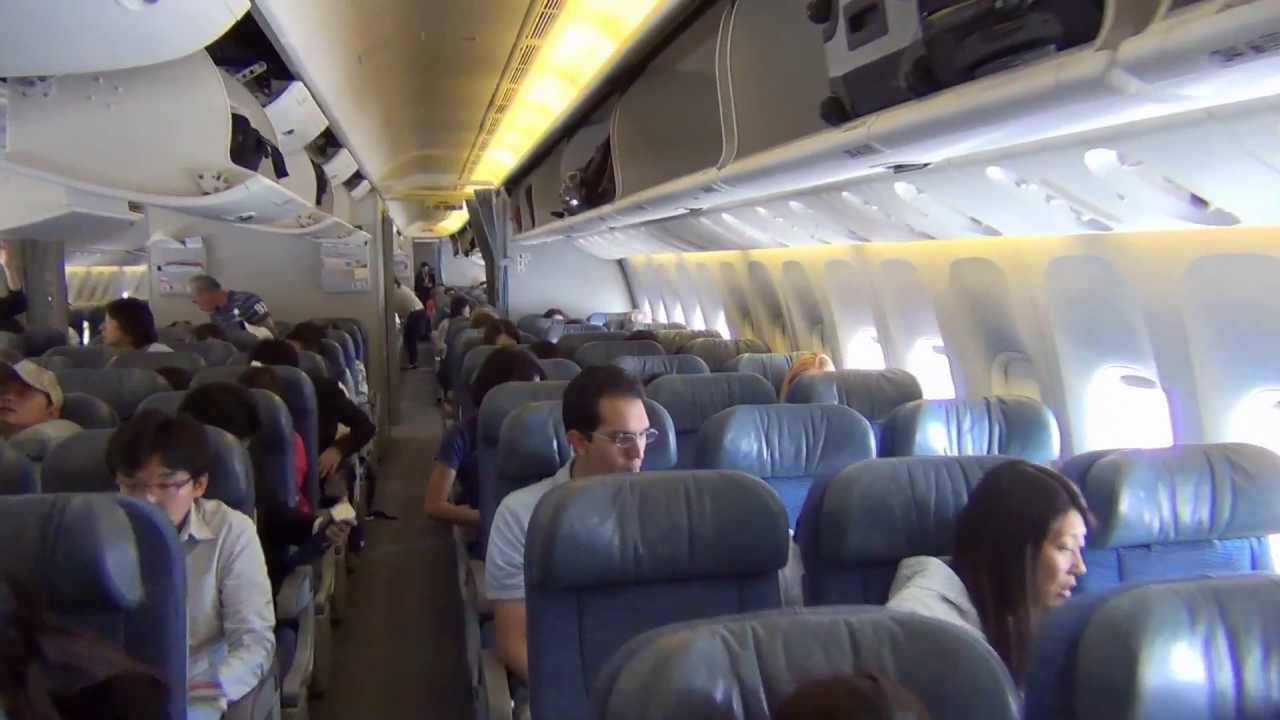
The above image shows the First Officer's (F/O) primary flight controls with yoke in the foreground and rudder pedals in the background below. On the right (outboard) horn of the yoke you can see the Autopilot (AP) disengage button and the Pitch Trim Switch (or rather, switches, both must be operated simultaneously) which I will discuss in more detail later on. For now it suffices to say that pushing the trim switches on the 777 will not directly move the stabilizer but will instead set the Trim Reference Airspeed (TRS). The concept of TRS is of capital importance to properly understanding how the 777's FBW System works. On any conventional aircraft such as the 737, operating the trim switch will move the pitch angle of the horizontal stabilizer (or horizontal tail-plane); it won't do quite the same on the 777.
Even though the pitch trim system internally works in a different manner with respect to a conventional airplane, it is used in the exact same way, that is, should the pilot find himself pushing the control column forward to keep his desired flight condition, pushing the trim 'up' (what is usually known as a 'nose down' command) will gradually reduce the required force on the control. The opposite goes if the pilot is pulling back on the control. Just like in any aircraft, the ship will be 'in trim' once the required force on the control column is zero.
System Architecture
The FBW system consists of the following basic components:
- Primary Flight Computers (PFC). There are 3 triple-redundant PFCs labeled L, C and R. The PFCs constitute the 'heart' of the FBW system.
- Actuator Control Electronics (ACE). There are 4 identical ACEs labeled L1, L2, C and R (roughly corresponding to the L, C and R hydraulic systems). The ACEs are basically analog to digital and digital to analog converters.
- Power Control Units (PCU), at the heart of which lay the Control Surface Actuators that physically move the control surfaces. The PCUs are electrically signaled but hydraulically powered.
- ARINC 629 Data Buses. The Bus transmits information among the various components of the system; essentially it's an information 'highway'.
The system works as follows (see figure above): The pilot generates an input signal by manipulation of the primary flight controls. This analog signal is received by the ACEs which digitalizes it and redirects it to the PFCs via the ARINC 629 Data Bus. The PFCs constantly gather and monitor information from a number of aircraft sources and will then generate actual control laws by 'enhancing' the received signal. The PFC-generated control command will then be sent back to the ACEs which will in turn convert it to an analog signal that the PCUs will use to move the control surfaces. When the Autopilot is engaged it communicates directly with the PFCs.
The functions that the PFCs implement are, just to mention a few:
- Slip/skid compensation for coordinated turns
- Thrust Asymmetry Compensation (TAC)
- Turn compensation (prevents altitude loss during turns)
- Configuration change compensation (flaps, gear etc.)
- Thrust change compensation
- Dutch Roll dampening (also known as yaw dampening)
- Pitch control and stability augmentation
- Protections: Overspeed, stall, bank angle etc.
In the cockpit, pilots have control of the system via two overhead switches: A capped 'PFCs disconnect switch' and a 'Thrust Asymmetry Compensation' push-button that disconnects it. These controls are left untouched in their respective 'auto' position during all normal operations. See top left corner on the image below:
Regarding system redundancy, there's plenty of it. Four ACEs to control the three different hydraulic systems. Three PFCs, any one of them being capable of flying the aircraft in its Normal Law. A Ram Air Turbine (RAT) will automatically deploy in the event of hydraulic pressure loss to provide sufficient hydraulic power to operate the basic flight controls. Should, in a highly unlikely event, both the RAT and all three hydraulic systems fail, there is still a mechanical backup connection from the cockpit control wheel to the number 4 and 11 spoiler panels, as well as an alternate mechanical connection to the horizontal stabilizer through the 'alternate pitch trim' control located left of the spoiler/speedbrakes lever (see image below).
The alternate pitch trim control always moves the stabilizer directly and is generally not used in normal operations. Should all four ACEs fail, then the alternate trim system will still be operational to control pitch and together with that the aircraft will be governable through the use of engine differential thrust. It has been shown that such a complete loss of hydraulic power, though highly catastrophic, can result in successful control and safe landing of the aircraft. See the 2003 Airbus A300 Baghdad incident.
Consult references 1 and 2 for more detailed descriptions of the system.
Operating Modes
Based on system status, there are three different operating modes or 'laws':
- Normal Law: Full system functionality. This is the desired operating mode.
- Secondary Law: Degraded mode with limited functionality. PFCs still provide Control Laws but Protection features are not available.
- Direct Law: PFC's are not available. System reverts to a direct 'pilot to control surface' logic. Direct Law can be reached by disconnecting the PFCs.
The airplane is flown most of the time in Normal Law. Should the PFCs detect inconsistent information among various sources or a sufficient number of failures, they will revert to Secondary Law which is a degraded operating mode. If the PFC's fail altogether, the system will revert to Direct Law, the 'lowest' operating mode. The aircraft handles very similarly in the Secondary and Direct modes, the difference being that in Direct Law the PFCs are not generating the control laws for the actuators. It's worth mentioning that the aircraft is perfectly flyable in both the Secondary and Direct modes, although it's not dispatchable in such a state.
Interestingly enough, the Direct Law of the 777 is even more 'direct' than in a conventional 737 because of the lack of Yaw Damping and other features that constitute separate systems in a 737 but that are 'built-in' into the PFCs of the 777. It's therefore an 'everything or nothing' kind of logic.
In the cockpit, the pilot can overview the status of the system through the 'Flight Controls' synoptic, accessible via the Multi-Function Display.
Flight Tests
Throughout this series of 'flight tests' performed in the simulator, I will analyze the different handling qualities of the aircraft in both the Normal and the Direct law.
Effect of Primary Flight Control Commands
As earlier discussed, the pilot controls roll via the control wheel, pitch via the control column, yaw via the rudder pedals and thrust via the thrust levers. All controls involve some sort of protection that won't easily let the pilot push the plane out of its flight envelope. The system is generally designed so as to require minimal pilot input during hand-flying operations; small and smooth control inputs will be enough to command the aircraft through most normal maneuvers.
The wheel controls: a set of outboard ailerons (locked-out during high-speed flight), a set of inboard flaperons (which function as a combination of flap and aileron), and two sets of outboard and inboard spoiler panels. Rolling the wheel commands, not a given roll attitude, but a roll rate instead. While the wheel is deflected a given roll rate will be obtained; once the wheel is released back to neutral, the achieved roll attitude (or bank angle) will be held. To roll out of the turn back to straight flight, the wheel must be rolled in the opposite direction to the turn, just to be released back to neutral once the wings are level.
The column controls pitch attitude, or rather, angle of attack. It does so by deflecting the elevators first in the desired direction, then moving the stabilizer so as to streamline the elevators. This is done for several reasons: It allows for full elevator authority in either direction and reduces drag and load on the elevator. For comparison, the column of a 737 controls the elevators exclusively; if the aircraft is trimmed incorrectly, the pilot might 'run out' of elevator authority.
The rudder pedals control the deflection of the rudder. Usually the pilots need not control the rudder directly since this is automatically managed for them through the PFC's compensation features. An exception would be handling during take-off, approach and landing; situations in which flying at a crab angle might be required. The 'yaw damper' and 'rudder ratio' functionalities of conventional aircraft are 'built-in' into the PFC-generated Control Laws providing dutch roll dampening and protection against excessive rudder deflection during high-speed flight. The Thrust Asymmetry Compensation (TAC) system also operates the rudder in the event of a thrust asymmetry (i.e., engine failure during take-off) via application of rudder trim.
Aileron and Rudder trim may be applied, if required, like in any conventional aircraft via the controls located on the lower pedestal. These controls are usually not used during normal operations. The same is not true for the Pitch trim, which is an important secondary flight control.
Effect of Trim Reference Airspeed (TRS)
The Flight Test performed in my video depicts the following considerations. TRS changes in Normal Law at 12:50 to 15:49 and Pitch Trim operation in Direct Law at 15:50 to 17:53. All tests flown with constant thrust and in clean configuration.
The first thing to mention here is that the Boeing 777 pitch trim operation is performed in exactly the same manner as it's performed in any conventional aircraft. When the pilot wants to relieve a 'pushing force', he trims 'nose down'; when he wants to relieve a 'pulling force', he trims 'nose up'. Note that trimming nose down actually means physically pushing the trim switches in the 'upward' direction.
As previously discussed, in Normal Law the trim switches on the yoke of the 777 don't directly position the horizontal stabilizer like they do on the 737 but set a target Trim Reference Airspeed (TRS) instead.
The Trim Reference Airspeed is defined as the target indicated airspeed that the aircraft will eventually, after dampening of the Phugoid Mode, fly at in the absence of any other control input. To achieve this, the PFCs will command both the stabilizer and the elevators in the way that's necessary for the aircraft to fly at the TRS, all other parameters such as configuration, thrust setting etc. considered.
The most important corollary deriving from this fact is that the aircraft need only be trimmed for speed changes. Any kind of flight maneuver and/or configuration change that does not involve a change in the target airspeed, does not require trimming by the pilot.
The trim switches hence work as a Trim Reference Airspeed control. Trimming nose down will increase the TRS, trimming nose up will decrease the TRS.
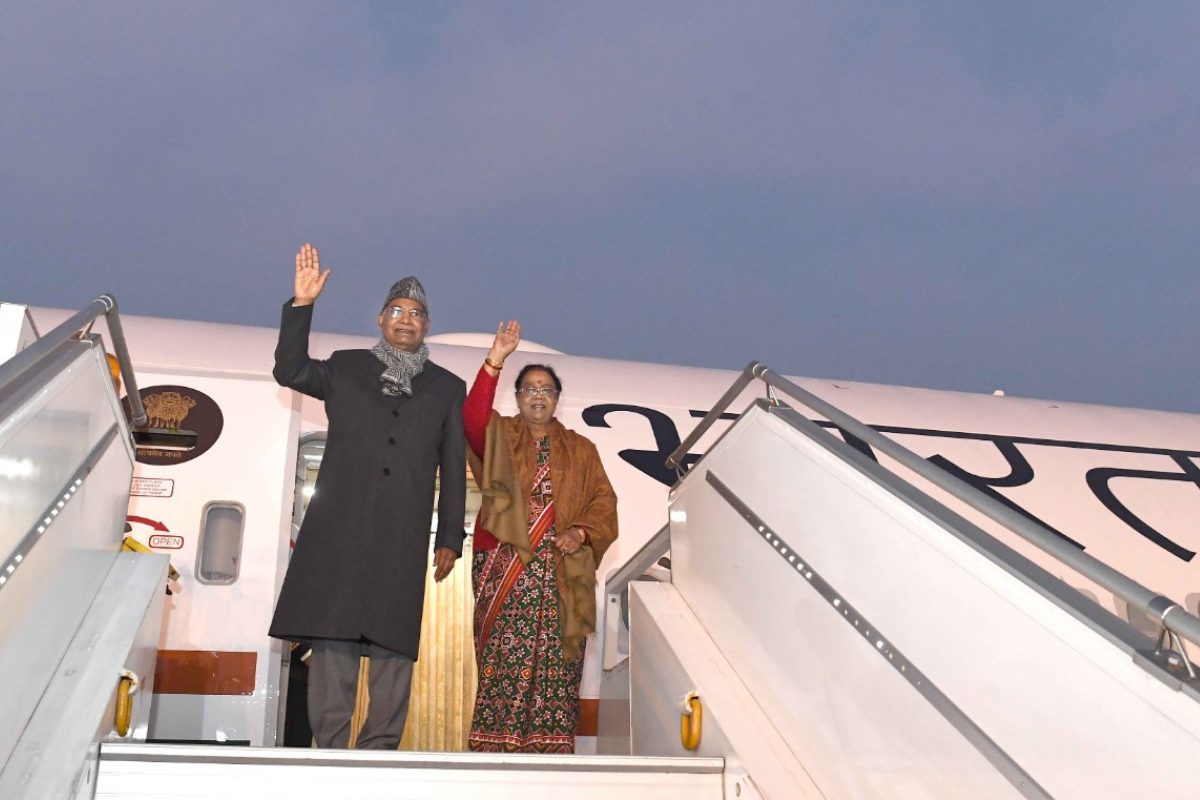
The above consideration remains true only when in Normal Law and while in flight. On the ground, or in Secondary or Direct mode, the pitch trim switches will move the horizontal stabilizer like in a 737.
Effect of Thrust (constant TRS)
See the Flight Test involving Thrust Changes at constant TRS at 17:54 to 21:44.
Since the Boeing 777 is a speed-stable aircraft (just like most conventional aircraft), for a given TRS the thrust levers are basically the 'up & down' control of the ship. Advance the levers and the aircraft will climb. Close the throttles and it will descend, always keeping the airspeed constant at the set TRS after the initial transition. For steady, unaccelerated 1-g flight, the angle of attack will remain constant as well.
Fly straight and level, trim the aircraft for the desired airspeed and stabilize the engines at around 50-60% N1. Now advance the thrust levers slightly. Initially the aircraft will tend to accelerate but the nose-up pitching moment generated by the excess thrust will raise the nose of the aircraft and prevent the speed from increasing. Since the PFCs are going to work their magic to bring the airspeed back to the unchanged TRS, all excess thrust is going to be employed into making the aircraft climb at the same airspeed and same angle of attack as in level flight.
Turn Compensation and Bank Limit Protection
See the Flight Test performed at 23:25 to 25:36 on Turns in Normal Law, and at 21:45 to 23:24 on Turns in Direct Law.
Starting from a straight and level flight condition, smoothly rolling the control wheel will command the aircraft to bank in the same direction. Releasing the wheel will stop the rolling and settle the attitude at the achieved bank angle. The aircraft will automatically compensate for slip by deflecting the rudder in the appropriate direction and will also compensate for pitch by trimming in a way that prevents the aircraft from losing or gaining altitude.
The Bank Angle Limit Protection prevents the aircraft from exceeding 35º of bank angle. For most normal operations, 25 to 30 degrees of bank are usually more than enough to perform a turn. If the pilot pretends to bank the aircraft past 35º, the sky pointer and slip indicator on the PFD (also known as 'sailboat') will turn solid amber, the control wheel will stiffen considerably and the PFCs will cease to compensate for a level and coordinated turn. Once the control wheel is released, the aircraft will roll back to 30º of bank.
B777 Flight Manual
Configuration Change Compensation
See the Flight Test regarding a lowering of the landing gear at 25:37 to 31:10.
In the pitch axis, the PFCs will automatically compensate for configuration changes in the usual manner: Deflection of the elevators followed by movement of the horizontal stabilizer to streamline the elevators.
In the event of a landing gear drop in straight and level flight, the Autothrottles will increase thrust to compensate for the increased drag. This thrust increase will generate a nose-up pitching moment which the PFCs will neutralize via nose-down commands to keep the aircraft in level flight.
A similar thing happens during flap deployment. Lowering the flaps will increase the lift and will tend to make the aircraft 'balloon' upwards. This will be prevented through nose-down corrections by the PFCs.
Approach to Stall and Full Stall
In these Flight Tests a 1-g Approach to Stall maneuver at 31:11 to 37:57 is performed followed by a Full Stall in Direct mode at 37:58 to 41:16.
The Boeing 777 incorporates an array of protections that make flying the aircraft into a stall very difficult. One must consciously and actively try to stall the aircraft to achieve it. The only way to 'fully stall' the aircraft in 1-g flight is to disarm the Autothrottles and disconnect the PFCs; both systems are supposed to stay armed/on during all normal operations.
As a first level of protection come the Autothrottles (ATs). When armed, the ATs won't let the airspeed drop below Minimum Maneuvering Speed (top of the amber bar on the speed-tape, see image above). If the ATs are disengaged and the speed drops below MMS, they will re-engage and push the thrust levers forward to accelerate back to MMS in a function called 'wake-up'.
Disarming the Autothrottles through the AT disarm switches on the Mode Control Panel (MCP) will prevent them from 'waking-up' at low airspeeds. In such a case the Autopilot, if engaged, will give up on maintaining level altitude and let the aircraft descend in an attempt not to exceed a given angle of attack. An aural and visual warning will alert the pilots of this.
When hand-flying, the pilot won't be able to trim the aircraft for a speed slower than Minimum Maneuvering Speed. The admissible range for the TRS is limited by the MMS on the lower end and the maximum operating speed Vmo/Mmo on the upper end. Flying at a speed slower than MMS will require the pilot to continuously pull on the control column. If he releases the control, the aircraft will drop the nose to accelerate back up to MMS.
If the pilot continues to pull on the column while the airspeed drops trying to fly level, at some point he will reach the red 'barber pole' and the stick shaker will activate warning the crew from the imminent stall. At maximum backwards control column deflection, the aircraft will not fully stall as the PFCs will limit the deflection of the elevators to a value such as to not exceed the maximum angle of attack and fully stall the aircraft. Stick shaker activation occurs when the angle of attack is slightly below the maximum value.
Fully stalling the aircraft requires disconnection of the PFCs to retain enough elevator authority so as to exceed the maximum angle of attack. Once in Direct Law with ATs disarmed and AP disengaged, the aircraft can be stalled just like any conventional aircraft.
Conclusion
The Boeing 777 is a formidable flying machine. Its Fly-By-Wire Flight Control System greatly enhances aircraft handling qualities, increases safety and reliability, reduces system weight and maintenance costs and lets the pilots have ultimate full authority over the ship at all times. And it achieves all that while still conserving the feel and handling principles of any conventional aircraft.
Relevant Software
- Microsoft Flight Simulator X - Windows-based Flight Simulation platform
- PMDG Boeing 777 - Complex and realistic simulation of the Boeing 777
B777 Flight Deck Pictures
References
B777 Flight Deck
- Gregg F. Bartley - The Boeing 777 Fly-By-Wire Flight Control System, Ch. 11 The Avionics Handbook (2001 CRC Press)
- Y. C. Bob Yeh - Triple-Triple Redundant 777 Primary Flight Computers (1996 Boeing Commercial Airplane Group)
- Major J.P. Sutherland - Fly-By-Wire Flight Control Systems (1968 Air Force Flight Dynamics Lab)
- Cooper, Harper - The Use of Pilot Rating in the Evaluation of Aircraft Handling Qualities (1969 AGARD Report 567)
- Boeing 777 Flight Crew Operating Manual (The Boeing Company)
- W. Langewiesche - Stick and Rudder. An Explanation of the Art of Flying (1944 McGraw-Hill)
- Karl Sabbagh - 21st Century Jet. The Making and Marketing of the Boeing 777 (1996 Scribner)